Due to the increasing population, urbanization, and consumption of goods, landfills are overflowing, illegal dumping is increasing and gigantic plastic soups are drifting in our oceans. About time we really start recycling our plastic waste. Let’s take a further look at the valuable materials plastic waste contains and how we can separate and reuse those efficiently.
Overview of content
Where does plastic waste go?
Recycle plastic waste to fuel
Dewater plastics and reuse the water too
Advantages of dewatering plastics
Dewater with the Organic Liquefying Press
The OLP versus conventional technologies
Where does plastic waste go?
Around 90% of all plastic waste (like separated plastic waste and plastic in paper pulp rejects) ends up at landfills, illegal dumping grounds, or oceans. That is much more than many would have us believe.
Did you know plastic takes almost 400 years to digest? Therefore it causes big capacity problems at landfills and an increase in illegal dumping grounds. These are often set on fire in the open air to avoid issues with the government.
An estimated 41% of all waste is burned like this, making up one-third of the total emission of particular pollution and five percent of all CO2 emissions. Furthermore, the open burning of plastic releases toxic emissions and causes serious health and climate issues.
Sources: Plastic Soup Foundation, National Geographic and National Center for Atmospheric Research
Recycle plastic waste to fuel
Though burning waste in an incinerator is a legal, more healthy, and climate-friendlier way to decrease the pressure on landfills, yet it’s a non-sustainable solution as valuable materials are lost.
By sorting the waste, various plastics and materials can be recycled. Moreover, chemical recycling techniques can turn the non-recyclable materials into energy or fuel. However, chemical recycling is a rather unsustainable solution because of the use of a lot of energy and even fossil fuels. Source: PowerTechnology
If we can reuse as many plastic fractions as possible, we can add more value to plastic and get one step closer to a circular plastics value chain. Could we, therefore, separate other valuable fractions from the plastic waste, which then can be reused sustainably?
Dewater plastics and reuse the water too
Yes, the plastic waste contains quite some moisture. Moisture increases weight causing unnecessary costs in areas as transportation (for recycling or to landfills), additional heating (for incinerators), and gate fees (landfills). The separation of the liquid from solid fractions of plastic is, therefore, beneficial for all plastic waste streams.
Furthermore, liquids are a valuable resource. (Waste)water can be turned into clean water or be reused in the production process. Hence we can enhance water security and sustainability.
Royal Dutch Kusters Engineering, therefore, developed a unique, reliable, and effective high-pressure separation technology to separate moisture from solid waste fractions in a smart and energy-efficient way. It can handle uncleaned plastics and plastic in paper pulp rejects, but also plastics in MSW, green waste and food waste.
Also read: Turning mixed waste into energy: Separate organics from solid and fibrous waste
Advantages of dewatering plastics
Before taking a closer look at this press, let’s discuss the exact benefits of recycling liquids and dry solid plastic fractions separately. Besides you reduce your environmental footprint, contribute to the circular economy, and the reduction of fossil fuel use, there are some additional benefits per application.
Paper pulp rejects, for example, include a large amount of non-recyclable plastics and contain around 70% of moisture. Through the separation of the plastics from the wet paper pulp, plastic rejects can be used as alternative energy due to their high calorific value.
The better the rejects are dewatered, the lower the weight, and thus the lower the transportation and gate fee costs. Moreover, less additional heating is required while turning the rejects into alternative fuel. The moisture, in turn, can be reused in the production process.
Also read: Optimise the dewatering of paper pulp rejects
Dewater with the Organic Liquefying Press
The question that remains is: How can we separate moisture from solid fractions? The Royal Dutch Kusters Engineering Organic Liquefying Press (OLP) can reduce 25 to 80% of weight in moisture, depending on the characteristics of the waste.
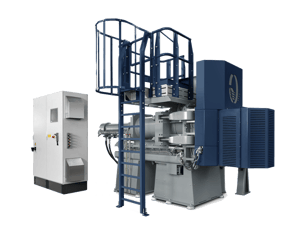
Moreover, the programmable smart press automatically optimises throughput and segregation. There are almost no restrictions on the input material.
Finally, the OLP has a robust design, remote monitoring, and predictive maintenance. An anti-jam mechanism avoids blockages and the OLP can alert the rest of the line if garbage separation has to stop. The OLP, therefore, allows for low downtime and higher process efficiency.
The OLP versus conventional technologies
Commonly used dewatering technologies, such as screw presses, generally show moderate drying results. Often, 40 to 60% of the moisture remains after pressing. By reaching a higher pressure per cm2, the OLP can deliver a more constant quality, resulting in better dewatering effects. This way, additional drying steps could be eliminated from your production process.
Keep informed on the latest insights and subscribe to our blog.